Capital and Concrete: This Week In Energy (July 7, 2025)
EDF Returns to UK Nuclear, Pentagon Secures Rare Earths, TerraPower Expands Natrium Supply Chain, Tulum Revives Hydrogen, Libya Reboots Oil, Argentina Fuels Up
In The Headlines
BP, Shell Ink Strategic Deals to Reboot Libya’s Oil Production (EN)
BP and Shell sign MoUs with Libya’s National Oil Corporation (NOC) to explore restarting major oil fields long idled by conflict, aiming to boost national output amid recent production gains
BP to study Sarir and Messla fields in the Sirte Basin, Shell targets Al-Atshan field near the Algerian border
Libya seeks to ramp up production to 1.6mm barrels/day by 2026 and 2mm by 2030, relying on foreign investment and technical partnerships to rebuild a fragile but vital sector
EDF Commits €1.3bn to UK’s Sizewell C Nuclear Project (EN)
EDF takes a 12.5% stake in Sizewell C, investing €1.3bn (~$1.4bn) in the UK’s second EPR plant during Macron’s London visit
Project includes two European Pressurized Reactors (EPRs); EDF joins UK government, Centrica, and Brookfield as key backers, with final financing terms expected this summer
UK has pledged £17.8bn (~$22.9bn), but private capital remains essential; Bpifrance also backing EDF with a €5bn (~$5.6bn) guarantee
Critics cite EDF’s smaller stake and past overruns at Hinkley Point C as warning signs, raising concerns over taxpayer exposure and long-term project risk
Pentagon Becomes Largest Shareholder in MP Materials with $400mm Investment (CNBC)
US Defense Department to invest $400mm in preferred stock, gaining a ~15% stake in MP Materials—the only operational US rare earth miner—sparking a 50% share price surge
Funding will support expansion of rare earth processing and a second US magnet plant, with DoD to purchase 100% of its output for 10 years
Pentagon guarantees $110/kg floor price for NdPr (used in magnets for F-35s, drones, submarines), with profit-sharing above that level once the new 10,000-ton facility goes live in 2028
$150mm DoD loan and $1bn in financing from JPMorgan and Goldman Sachs back full supply chain reshoring, seen as a model for public-private defense-critical investments
Brookfield, Stonepeak, Air Liquide Advance in $3.6bn DIG Airgas Sale (Reuters)
Macquarie AM shortlists Brookfield, Stonepeak, and Air Liquide for final bids on DIG Airgas, South Korea’s #3 industrial gas producer
Sale could fetch up to $3.6bn, valuing DIG at 18–20x EBITDA (~$170–180mm), according to sources; Goldman Sachs and JPMorgan advising on the process
Brookfield previously acquired SK Airplus in 2022; this deal would mark Brookfield and Stonepeak’s largest Korea investment if successful
Nano Nuclear, UrAmerica Partner to Develop Argentina’s Uranium Supply Chain (NucNet)
Nano Nuclear (US) signs MOU with UrAmerica (Argentina) to explore uranium mining, ore processing, and UF₆ conversion, targeting supply chain integration for US-bound nuclear fuel
UrAmerica holds exploration licenses in Chubut’s San Jorge Basin, home to one of Latin America’s largest untapped uranium deposits
Talks include potential purchase agreements, fuel cycle infrastructure investments, and joint ventures, aligned with Argentina’s push to partially privatize its nuclear sector
Argentina aims to boost nuclear capacity under President Milei, who backs new reactor builds to power advanced tech; country holds 80,000 tU in estimated reserves
Hitachi Unveils Metaverse Platform to Digitize Nuclear Plant Operations (Hitachi)
Hitachi launches a metaverse-based platform combining 3D CAD, point cloud data, and AI to create digital twins of nuclear plants, enabling real-time collaboration, planning, and maintenance
Serves as core of Hitachi’s “Data-Driven Power Plant” vision, using analytics to optimize investment, predict equipment failures, and enhance operational reliability
Developed under Lumada 3.0 with GlobalLogic, the tool targets construction, maintenance, safety, and decommissioning phases for utilities facing demographic and regulatory pressures
Launchpad: Energy Startup Activity
TerraPower Awards More Supplier Contracts for Natrium Reactor Project (Terrapower)
TerraPower selects three new US-based suppliers—AVANTech, Structural Integrity Associates, and PAR Systems—for advanced systems in its 345 MWe sodium-cooled Natrium reactor, under construction in Wyoming
Contracts include systems for sodium processing, gamma spectroscopy radiation monitoring, and spent fuel pool handling, supporting the Natrium plant’s safety and operability
All long-lead items and the full reactor enclosure have been awarded, signaling strong progress in building a resilient domestic advanced nuclear supply chain
Backed by the DOE’s ARDP program, the plant will feature molten salt energy storage to flex from 345 MW to 500 MW, with commissioning targeted for 2030
Shine and Standard Nuclear Partner to Recycle Used Fuel for TRISO Supply (ANS)
Shine and Standard Nuclear form a 1-year partnership to explore recycling spent fuel into uranium, plutonium, Sr-90, and Am-241 for TRISO and nuclear batteries
Shine plans a 100-metric-ton/year facility by early 2030s, aiming to scale recycling across the US’s 90,000-ton spent fuel stockpile
Standard Nuclear acquired USNC’s TRISO assets, positioning itself as a reactor-agnostic fuel supplier for advanced fission and defense use
Partnership supports the May 23 Trump EO making fuel recycling official US policy, boosting domestic fuel security
Tulum Energy Revives Accidental Methane Pyrolysis Discovery with $27mm Seed Round (TechCrunch)
Tulum Energy spun out of Techint Group to commercialize an electric arc furnace splitting methane into hydrogen and solid carbon
Unlike competitors (e.g., Modern Hydrogen, Monolith), Tulum’s process requires no expensive catalysts and repurposes modified steel-industry tech for low-cost, scalable deployment
Backed by $27mm seed funding from TDK Ventures, CDP Venture Capital, and others, Tulum will build a pilot plant in Mexico next to a Techint steel facility
At scale, aims to produce 200 tons/day of H₂ and 600 tons/day of solid carbon at $1.50/kg in the US, undercutting many green hydrogen pathways while avoiding CO₂ emissions entirely
Google, Meta Back $41mm Bioenergy with Carbon Capture and Storage (BECCS) Deal with Arbor (CarbonCredits)
Frontier coalition (Google, Meta, Shopify, etc.) commits $41mm to purchase 116,000 tons of CO₂ credits from Arbor’s first BECCS plant in Louisiana (2028–2030), Arbor’s largest offtake to date
Arbor’s modular oxy-combustion system captures >99% CO₂ and powers an 18 MW turbine, offering carbon-negative, energy-positive baseload power for AI/data center needs
Units convert biomass waste to energy and removals, delivering up to 1,000 kWh per ton of CO₂ captured with no particulate or NOx emissions
Deal helps bridge Arbor to commercial scale, aligning with a broader shift toward permanent, verifiable CO₂ removals and setting a benchmark in the voluntary carbon market
Nuclear Heat Exchanger Materials (HXMs) – A Deep Dive
Role and Purpose of Heat Exchangers in Nuclear Reactors
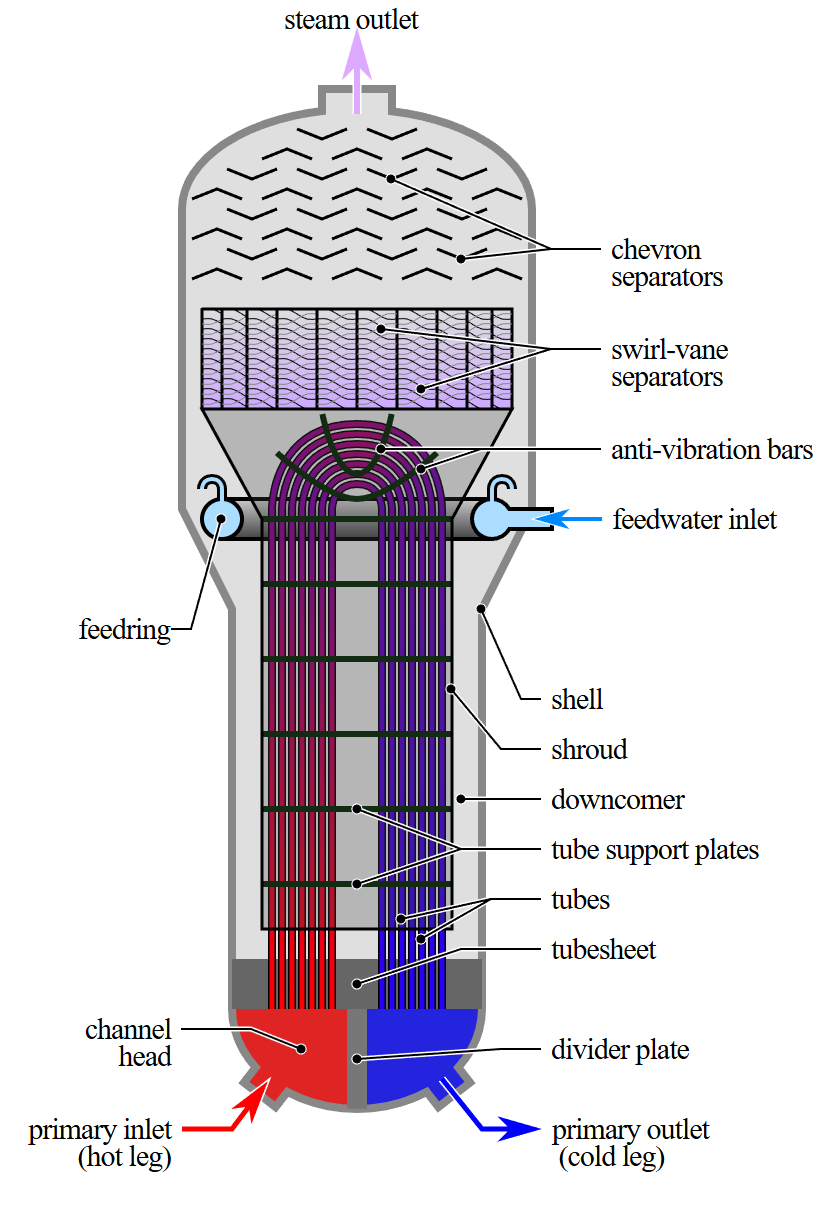
In nuclear power plants, a heat exchanger is a critical interface between the reactor core and the power-generating cycle. In PWRs, this takes the form of a steam generator – a large shell-and-tube heat exchanger that uses the reactor core’s hot, pressurized water (primary coolant) to convert feedwater in a secondary loop into steam. The primary coolant, heated by the nuclear fuel, flows inside thousands of thin tubes within the steam generator. As it passes through, its heat is conducted through the tube walls to boil the surrounding secondary water into steam. This indirect heating allows the secondary steam to drive a turbine and generator to produce electricity, all while the radioactive primary water remains sealed inside the tubes. The steam generator tubes thus serve as a safety barrier, ensuring that radioactive fluid from the core does not contaminate the steam that exits to the turbine and environment. In fact, the tubes are one of multiple containment barriers in a PWR, preventing fission products from reaching the outside world under normal operation.
Using an intermediate heat exchanger has several purposes: it isolates the reactor coolant from the turbine loop (protecting the turbine from radiation and corrosion), and it allows different pressures or coolants to be used for optimal reactor and turbine performance. For example, PWR primary water is kept at very high pressure to avoid boiling in the core, whereas the secondary side operates at a lower pressure where water can boil to steam. The heat exchanger enables this coupling of different conditions. It also means that if steam needs to be vented or a turbine component leaks, it’s non-radioactive steam, which is a major safety advantage.
Not all reactors use such a two-loop setup. Boiling water reactors (BWRs), for instance, do not have a separate heat exchanger between the core and turbine – they boil water directly in the reactor vessel and send that steam to the turbine. This direct cycle simplifies the design and improves thermal efficiency (no intermediate heat transfer losses). However, it means the turbine and condenser system must handle fluid that has been in the reactor, which carries short-lived radioactivity (e.g. N-16 in the steam) and necessitates shielding and careful maintenance. Most other reactor designs (e.g. PWRs, CANDU heavy-water reactors, sodium fast reactors, molten salt reactors) adopt indirect cycles with heat exchangers, trading some efficiency for the safety and flexibility benefits of keeping the radioactive coolant contained within a primary loop.
Types of Heat Exchanger Materials and Their Pros & Cons
Materials used in nuclear heat exchangers (HXMs) must withstand extreme conditions: high temperatures, high pressure differentials, intense radiation fields, and chemically reactive coolants. Over the decades, engineers have developed several classes of alloys for these duties. Key material properties of interest include creep resistance (to avoid slow deformation at high temperature), corrosion resistance (against water, salts, or liquid metals attacking the material), and thermal fatigue strength (to survive repeated heating and cooling cycles without cracking). Below we outline the main categories of HXM materials, with their typical applications, advantages, and drawbacks:
Austenitic Stainless Steels (e.g. 304, 316 series)
These iron-based alloys (with high chromium and nickel content) were among the first materials used in nuclear heat exchangers and still see use in some reactor systems. They are the same family of stainless steels common in industrial boilers and piping.
Pros: Excellent general corrosion resistance in water and steam environments due to their protective chromium oxide layer. They are tough and ductile, even at low temperatures, and easy to fabricate and weld. Stainless steels performed adequately in early reactor steam generators (e.g. a few 1960s units used Type 316 tubing). They also show good thermal fatigue resistance owing to their ductility – they can expand and contract without cracking if properly designed
Cons: Austenitic steels have limited high-temperature capability – above ~550 °C their creep strength drops off, meaning they can gradually deform under stress over long periods. This makes them less suitable for advanced reactors with very high outlet temperatures. They are also susceptible to certain forms of corrosion in nuclear service. Notably, stress-corrosion cracking (SCC) can occur if the environment has impurities or tensile stresses. For example, chloride or oxygen in water can induce cracking in 304/316 steel under stress. In fact, a primary reason stainless steel tubing was mostly phased out in favor of nickel alloys in light-water reactors was to mitigate corrosion cracking issues. Additionally, stainless steels can suffer radiation-induced swelling in core environments (though in a heat exchanger outside the core this is less of an issue). Overall, their use in modern reactors is usually limited to moderate temperatures or secondary-side components, or in environments like sodium coolant where oxygen is absent and corrosion is minimal.
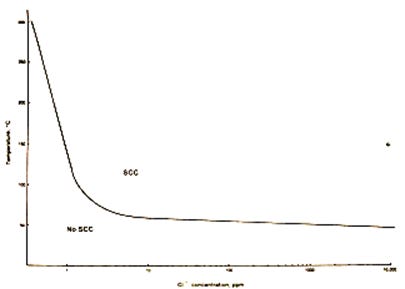
Nickel-Based Alloys (e.g. Inconel 600/690, Incoloy 800, Hastelloy family)
Nickel-chromium alloys have become the workhorse materials for PWR steam generator tubing and are strong contenders for next-generation reactor heat exchangers. These alloys include Inconel (primarily Ni-Cr-Fe), Incoloy 800 series (Fe-Ni-Cr), and Hastelloy or other Ni-Mo-Cr alloys.
Pros: Nickel-based alloys offer superior corrosion resistance in both water and other aggressive environments. In PWR steam generators, Alloy 600 (Ni~75%, 15%Cr, 10%Fe) was originally used because it resisted general corrosion better than stainless steel. Later, Alloy 690, with ~30% chromium, became the preferred tubing material specifically to overcome stress-corrosion cracking problems – its higher chromium content makes it much more resistant to cracking and wastage in hot water chemistry. Today, the vast majority of PWRs use thermally treated Alloy 690 tubing, which has shown no observable SCC in service (unlike its Alloy 600 predecessor). Beyond water reactors, certain Ni alloys can tolerate very high temperatures: for example, Alloy 617 and Alloy 230 have been identified as suitable for intermediate heat exchangers operating around 900 °C in helium-cooled reactors. Ni alloys maintain their strength well at elevated temperatures and often form stable oxide layers that protect against oxidation and corrosion in gas, salt, or liquid metal environments. In molten salt reactors, a special Hastelloy (Nickel-Molybdenum alloy Hastelloy-N) was developed to resist hot fluoride salt corrosion – it was used successfully in the Molten Salt Reactor Experiment for piping and the primary heat exchanger, operating at ~650 °C. Overall, Ni-base materials are highly versatile and have become synonymous with nuclear heat exchanger service in harsh conditions.
Cons: The primary downsides of Ni alloys are cost and manufacturability. They are more expensive than common steels and can be harder to machine or weld (due to strength and nickel’s tendency to work-harden). Some Ni alloys also have specific weaknesses that must be managed. For instance, a given alloy optimized for one extreme may sacrifice performance in another area – Alloy 602CA can be qualified up to 982 °C, but its allowable stress at those temperatures is relatively low, meaning thicker sections or lower loads are required. Another example is Alloy 556, which has very high strength but was found to have inferior resistance in certain nitriding environments (e.g. impure helium) compared to alloys like 617 or X. In corrosive coolants, even Ni alloys need sufficient chromium or molybdenum content to avoid attack (e.g. for liquid salt or lead coolant, Ni alloys or advanced stainless grades with protective coatings are needed to avoid rapid corrosion). In summary, while Ni-based HXMs excel in performance, engineers must choose the specific grade carefully for the given coolant chemistry and temperature. The material and fabrication costs also tend to be higher, which is a trade-off for their longevity and reliability.
Ferritic/Martensitic Steels (e.g. Grade 91 (9Cr-1Mo-V), HT9)
These are low-carbon steels with high chromium (9–12%) and added molybdenum/vanadium, often referred to as “creep-resistant ferritic steels” or Cr-Mo steels. They have a different crystal structure (body-centered cubic) than austenitic stainless, giving them distinct properties. Ferritic/martensitic alloys have seen use in advanced reactor heat exchangers, especially in liquid metal fast reactors and some high-temperature components.
Pros: Ferritic/martensitic steels are prized for their high-temperature strength and creep resistance. For example, modified 9Cr-1Mo steel (ASTM Grade 91) retains excellent mechanical strength for continuous service up to around 600 °C, making it ideal for superheater tubes in conventional fossil boilers and for sodium-cooled reactor heat exchangers. These steels typically have a tempered martensite microstructure with strengthening carbides, which gives them a high creep-rupture life. They also have a lower coefficient of thermal expansion compared to austenitic alloys, which means lower thermal stresses when temperatures fluctuate. This, combined with good thermal conductivity, imparts better thermal fatigue resistance – indeed, Grade 91 and similar alloys are noted to exhibit resistance to thermal fatigue cracking under cyclic operation. In sodium fast reactors, both 316LN austenitic steel and modified 9Cr steel have been used for intermediate heat exchanger tubing; the 9Cr steel showed virtually no corrosion or dimensional change after long-term sodium exposure at ~525 °C, indicating excellent compatibility (sodium is non-oxidizing). Additionally, ferritic steels are magnetic and easier to ultrasonically inspect for flaws (a minor perk for in-service inspection). They are also relatively economical compared to high-nickel alloys.
Cons: The trade-off for ferritic/martensitic steels is reduced corrosion resistance in environments like water or steam unless carefully managed. Unlike stainless steel, a 9Cr steel can rust or oxidize appreciably if exposed to oxygenated water. (In PWR steam generators, early designs that used carbon steel support plates saw those plates corrode; the corrosion product buildup dented the tubes until the industry switched to stainless support plates – a cautionary tale about using ferritic steel in wet, oxygenated conditions). Thus, ferritic alloys are best used in inert environments (like liquid sodium, or gas coolant with controlled oxygen) or with protective coatings. Another concern is temper embrittlement and phase instability over long periods. These steels can form brittle precipitates (such as Laves phase or carbides) after thousands of hours at temperature. For instance, modified 9Cr-1Mo, after very long exposure in service, can experience a drop in impact toughness due to such aging effects. This means careful heat treatment and possibly periodic surveillance of mechanical properties are needed for very long-life components. They are also less ductile than austenitics at room temperature, so welding procedures must be controlled to avoid cracks (Grade 91 requires preheat and post-weld heat treatment to prevent weld embrittlement). In summary, ferritic/martensitic HXMs shine in high-heat, high-stress roles, but they are not a universal solution – they require environmental control to prevent corrosion and careful metallurgical management to avoid long-term embrittlement.
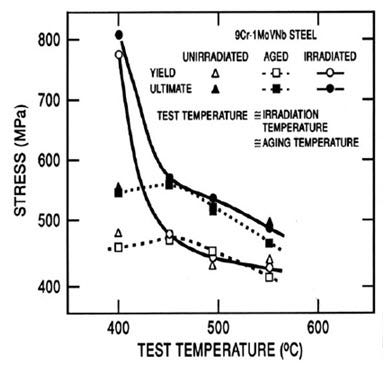
Advanced Alloys and Composite Materials (ODS steels, Ceramics)
Pushing reactor outlet temperatures towards 800–1000 °C (as envisioned in some Gen-IV reactors and industrial heat applications) is beyond the reliable limits of conventional metal alloys. This has led to research on advanced materials like oxide dispersion strengthened (ODS) alloys and ceramic composites for heat exchangers.
Pros: ODS alloys are metallic steels or Ni-base alloys infused with tiny oxide particles (e.g. Yttria) that block dislocation creep. They can maintain strength at higher temperatures than their conventional counterparts – some ODS steels have demonstrated usable creep strength in the 700–800 °C range, extending the metallic service window. Ceramic-based HX materials (such as silicon carbide composites or refractory alloys) offer the potential for exceptional corrosion and heat resistance – ceramics don’t suffer traditional metal corrosion and can operate at temperatures well above 1000 °C. For instance, silicon carbide heat exchanger panels have been considered for very high temperature gas reactors (since SiC has low neutron activation and can handle hot helium). These advanced materials could enable heat exchangers for processes like hydrogen production that involve corrosive chemicals at high temperature. From a performance standpoint, they promise to significantly increase the allowable temperature, thus improving thermal efficiency or enabling new reactorcoolant chemistries without material failure.
Cons: Brittleness and validation challenges are the big hurdles. Ceramics (like SiC) are very strong in heat but also very stiff and brittle – they can shatter under mechanical or thermal shock loads, which is a stark contrast to the forgiving nature of metals. This makes design against sudden stress difficult. Joining and assembling ceramic heat exchangers is non-trivial (special adhesives or mechanical joints are needed, since standard welding is out). ODS alloys, while metallic, are difficult to fabricate and weld (the very oxides that strengthen them can disrupt welding). Furthermore, codes and standards currently have limited allowances for these materials; nuclear pressure vessel codes (ASME) historically cover conventional steels and Ni alloys. If a reactor project wanted to use a ceramic heat exchanger, new qualification and design rules would be needed. The manufacturing quality control for these materials is also challenging – ensuring consistency of an ODS alloy or integrity of a ceramic component over large areas is harder than for conventional metal tubing. In short, advanced materials show great promise for extreme service, but they are still largely in the R&D or prototype phase. Any near-term reactor designs will likely use improved traditional alloys (perhaps in combination with coatings) while these exotic materials continue to be developed and certified for future use.
Challenges in Extreme Environments: Creep, Corrosion, and Thermal Fatigue
Designing nuclear heat exchangers is an exercise in managing long-term material degradation. The key degradation mechanisms are creep, corrosion, and thermal fatigue – each can shorten the life of HXM components if not properly addressed:
Creep (High-Temperature Deformation): Metals will slowly and permanently deform if subjected to stress at high temperature over time. In a reactor heat exchanger, tubes and structures are under stress from pressure and thermal expansion. If the operating temperature is a significant fraction of the alloy’s melting point, creep becomes inevitable. Engineers choose materials and design thicknesses such that the estimated creep strain or creep rupture life will exceed the component’s life by a wide margin. For example, current ASME code limits effectively restrict standard stainless steels to ~temperature ranges where creep is minimal for the design life (PWR steam generators ~ 280–320 °C on the secondary side, where creep of Alloy 690 is negligible). But advanced reactors aiming for 900 °C outlet will inevitably run in the creep regime for even the best high-temperature alloys. In those cases, creep-fatigue interaction must be considered – the material can weaken over decades of steady load (creep) and also see cyclic loads. Designers account for this by using materials with known creep resistance (e.g. adding molybdenum and carbide formers to improve creep strength) and by qualifying the material with extensive creep tests. If necessary, they’ll turn to specialty solutions like ODS alloys or design the component to be replaceable after a certain service time. Creep is a slow damage mechanism, but it’s relentless – thus understanding an alloy’s long-term creep behavior is vital for nuclear HXMs.
Corrosion and Chemical Attack: Heat exchanger materials face chemical wear from whatever fluids they touch. Water-side corrosion was historically a big issue – for instance, in the 1970s many PWR steam generator tubes experienced wall thinning due to aggressive water chemistry, until water chemistry was adjusted. Corrosion can manifest as general thinning, pitting, or stress-corrosion cracking, among other forms. In light-water reactors, a primary concern became stress-corrosion cracking of Alloy 600 tubes, which was mitigated by switching to high-Cr Alloy 690 and by thermal treatment of tubing to stabilize its microstructure. In fast breeder reactors using liquid sodium, the coolant itself doesn’t oxidize steel (no oxygen), but it can cause dissolution of certain elements or carburization. Materials like 316 stainless have seen carbon ingress from sodium and some nickel leaching, which can embrittle the material over long periods – so controlling carbon activity in sodium and using compatible materials (or even liners/coatings) is important. Molten salt coolants are extremely corrosive to most common alloys because they can leach away protective elements like chromium. That’s why Hastelloy-N and similar nickel alloys with carefully balanced chemistry were developed; even so, developers must closely monitor salt purity (to remove moisture, oxygen, etc. that accelerate corrosion). Gas-cooled reactors avoid liquid-phase corrosion, but if the gas contains impurities (O₂, CO₂, sulfur compounds), it can oxidize or carburize the heat exchanger. For example, CO₂ coolant in the UK’s AGR reactors led to oxidation/carburization of 316 stainless steel boiler tubes over time, requiring strict control of gas chemistry. Overall, corrosion is tackled by selecting corrosion-resistant materials (alloys with enough Cr, Ni, Mo to form stable oxide scales or resist dissolution) and by controlling coolant chemistry (pH, oxygen content, impurities) within narrow limits. Periodic inspections are mandated to catch any corrosion before it compromises tube integrity. In short, corrosion dynamics in each environment dictate which HXM material will last: the material must form a protective film (oxide or similar) that equilibrates with the coolant without degrading further.
Thermal Fatigue: Nuclear systems experience temperature changes during start-ups, shutdowns, power swings, and even local fluctuations during steady power (for instance, as fluid mixes with different temperatures). These thermal cycles cause components to expand and contract. If a component is constrained or has non-uniform temperature, these cyclic expansions create stress cycles that can initiate cracks over time (similar to how repeated bending can break metal). Heat exchanger tubing and headers are particularly vulnerable at points where hot and cold streams create temperature gradients (like near welds or joints between thick and thin sections). To combat thermal fatigue, designers try to minimize steep temperature differentials and limit rapid transients. Materials with high thermal conductivity and lower expansion (like ferritic steels or certain composites) help reduce thermal gradients. Also, smooth geometries and good support of tubes prevent stress concentration points that could start a crack. The industry also employs fatigue usage factor calculations: every expected thermal cycle (e.g., heatup or cooldown of the plant) is counted toward a fatigue damage budget. Components are designed so that the total fatigue usage stays below 1 (i.e., below the endurance limit of the material) over the reactor’s life. Modern heat exchangers, such as compact diffusion-bonded ones, have shown excellent thermal fatigue performance – for example, testing of a printed-circuit heat exchanger design showed it had fatigue life well beyond required nuclear service levels. This indicates that with proper engineering, thermal fatigue can be managed such that it does not lead to failure in service. Nonetheless, operators remain vigilant: unexpected temperature oscillations (due to flow instabilities or mixing of hot and cold streams) have caused thermal fatigue cracking in some plant piping and smaller heat exchangers in the past. Thus, monitoring and design against thermal fatigue is an essential part of ensuring HXM longevity.
In summary, creep, corrosion, and thermal fatigue are the “big three” degradation modes for heat exchanger materials in reactors. Robust design, material selection, and operational controls (chemistry and procedures for heatup/cooldown) all work in concert to mitigate these issues. The goal is to have the heat exchanger last for decades (often the design life is 40–60 years for large reactor components) while maintaining safety margins.
Importance of Material Selection – Why It Matters
The choice of heat exchanger material is not just a technical detail; it can make or break the viability of a reactor design. Safety is the foremost concern: the heat exchanger (like the steam generator tubes) often forms part of the primary pressure boundary and the fission product barrier. A material failure could lead to coolant leaks or, worse, a breach that lets radioactivity escape. For instance, a steam generator tube rupture in a PWR could allow primary coolant to rapidly escape and even spray radioactive water/steam outside containment. While plants are designed to handle a single tube rupture safely, prevention is far better. The materials must therefore have high integrity and reliability under all expected conditions. This is why regulators require extensive testing and inspections of these components.
Historical experience has shown the consequences of suboptimal material performance. In the early days of PWRs, the prevalent Alloy 600 steam generator tubes suffered various corrosion problems – thinning of tube walls, denting from corroded support plates, and stress-corrosion cracking – which forced many plants into costly outages for inspections and replacements. Some reactors had to replace their steam generators entirely after just a decade or two of operation; a few even shut down permanently because of widespread tube degradation that was uneconomical to fix. This drove home the lesson that investing in better materials (like Alloy 690 tubing and improved support plate materials) was worth the up-front cost to avoid long-term operational issues. Indeed, since making those changes, the incidence of tube corrosion problems dropped dramatically, improving plant reliability and safety.
Beyond safety, there is an economic and performance impact. A more corrosion-resistant, creep-resistant material can allow a heat exchanger to run at higher temperatures or for a longer time between maintenance. Higher temperature capability, in turn, can boost the plant’s thermal efficiency (extracting more electricity from the same heat). For example, advanced reactors that use supercritical CO₂ or helium turbines demand very hot coolant – without materials like Alloy 617 or ceramics to handle ~800–900 °C, those reactor concepts simply wouldn’t be feasible. Thus, materials enable innovation: the development of HXMs often sets the timeline for next-generation reactors. Conversely, if a material is poorly chosen and requires early replacement, it can be extremely expensive. Replacing a steam generator in a large PWR is a massive operation costing tens to hundreds of millions of dollars. Therefore, getting the materials right from the start is crucial for the plant’s economic life.
Finally, material selection matters for regulatory and environmental reasons. A robust material that resists degradation will reduce the likelihood of unplanned releases of radioactivity and minimize nuclear waste (since components won’t need to be replaced and disposed of as often). It also gives regulators confidence in the long-term safety case of the reactor. In summary, HXMs are a cornerstone of nuclear plant safety, durability, and efficiency – seemingly subtle differences in alloy chemistry can have outsized effects on a reactor’s performance and public trust.
Reactor Designs Without Separate Heat Exchangers (Direct vs Indirect Cycle)
Given the challenges and complexity associated with heat exchangers, one might ask: can we eliminate them? As noted, BWRs already do this by using a direct steam cycle – the reactor water boils in the core and the generated steam goes straight to the turbine. This design choice has some clear advantages: it avoids the cost and large footprint of steam generators, and there’s no temperature loss across an intermediate heat exchanger (improving efficiency slightly). The system is simpler – only one coolant loop instead of two – which also made early BWRs quicker to construct than PWRs. However, the disadvantages manifest in operations and maintenance. The turbine and all steam piping in a BWR become mildly radioactive because the steam has passed through the core. (Oxygen in water gets activated to radioactive nitrogen-16, and trace contaminants or corrosion products can become activated and carry over.) This means the turbine hall of a BWR requires radiation shielding and careful access controls, unlike a PWR where the secondary loop is “clean.” Maintenance on BWR turbine components must account for radiation exposure to workers, which can complicate repairs. Additionally, the direct cycle requires very pure water and careful chemistry control to avoid carrying impurities into the core (since anything in the water goes through the reactor).
In advanced reactor concepts, engineers have explored direct-cycle designs to improve efficiency, but they must balance them against safety. For example, the PBMR (Pebble Bed Modular Reactor) design was a helium-cooled reactor intended to drive a gas turbine directly with the hot helium from the core, rather than exchanging heat to a secondary gas loop. The appeal is higher thermal efficiency and no large heat exchanger needed in between. But the drawback is that the turbine and compressor would be handling radioactive helium from the core, effectively becoming part of the nuclear boundary. This raises questions about maintenance and accident scenarios (any turbine leak could potentially release radioactive gas). On the other hand, an indirect cycle (with a heat exchanger) keeps the turbomachinery non-nuclear at the expense of adding a heat exchanger and some thermal loss. One study comparing direct vs. indirect helium Brayton cycles noted that using an intermediate heat exchanger improves safety by isolating the loops, but adds significant mass/complexity (the heat exchanger mass could be 30–60% of the entire system) without a big efficiency gain. This highlights the trade-off: indirect cycles are heavier and a bit less efficient, but they confine radioactivity to the primary loop, which is a major safety advantage.
In summary, there are nuclear reactor designs without traditional HXMs – chiefly BWRs and some theoretical gas reactor designs – and they offer simplicity and efficiency perks. However, they introduce other challenges: the power conversion equipment must be nuclear-grade and radiation-tolerant, and any leaks or failures in that equipment can directly involve radioactive material. Thus, many reactor designs opt for indirect cycles with heat exchangers despite the complexity, because they act as buffers protecting the turbine and the public. Each approach (direct vs indirect) has its merits, and the choice depends on the specific goals and constraints of the reactor design. What’s clear is that even if a reactor has “no heat exchanger,” the materials in its primary circuit still must handle extreme conditions – so there is no escaping the need for advanced, robust materials in any nuclear system that aims for safe, long-term operation. The story of nuclear HXMs is ultimately about engineering materials to enable the reactor’s heat to be harnessed efficiently and safely, whether that heat is transferred across a dedicated exchanger or used directly in a turbine.
Cool article on nuclear heat exchangers! It’s neat to see how they use stuff like nickel alloys to handle the intense conditions and keep things running safely.